
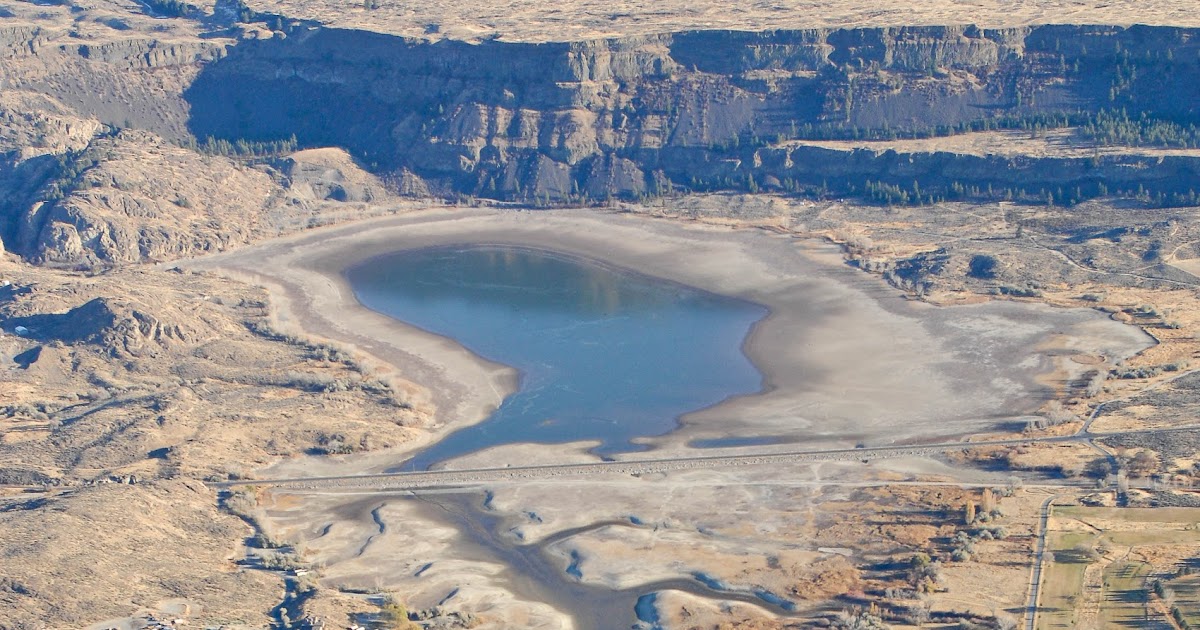
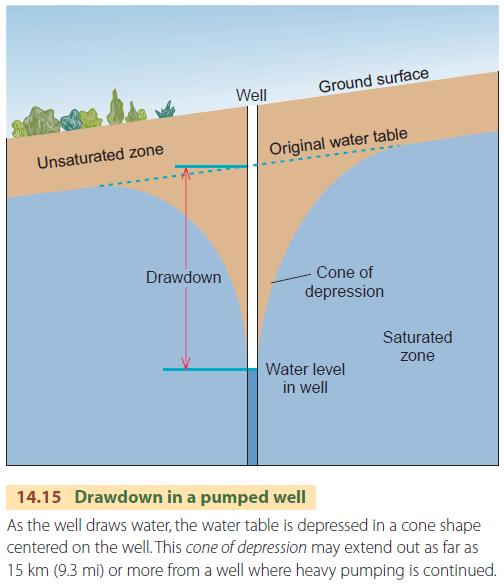
This is usually done with a hydraulic system designed and built to provide closing power to the equipment in 5 sec or less and to maintain the required pressures as desired. The accumulator system provides closing energy to all members of the BOP stack. Note that this design does not constitute a true diverter system.Īccumulator Systems. A direct line from the preventer stack to the burning pit for gas is provided should it become necessary to divert the well temporarily.
#WELL DRAWDOWN TEST EASTERN WASHINGTON MANUAL#
A current, and more appropriate, practice is to use two remote hydraulic adjustable chokes and a single manual chokc. Two h and-adjustable chokes may be provided due to their high stem and seat erosion rates and due to their tendency to pack off with cuttings. A tap may be provided to allow for manifold pres-surization to prevent pressure surges when opening the valves near the stack. Buffer chambers are used at the downstream connections to act as hydraulic cushions and to minimize erosion. Note that this design meets all of the requirements for choke manifolds. 16-69 illustrates a choke manifold used in many drilling operations. Also, it is a good practice initially to use the manifold necessary to reach the total depth to avoid installing a different manifold with each casing setting depth.įig. The proper procedure is to ensure that a backup system is available should the primary tool fail. The principle applied to blowout preventer stack design also will be applied in designing the choke manifold. All lines and valves should have the same consistent inner diameter to minimize turbulent erosion at diameter changes. The choke should feature easy access to every manifold component, with all lines constructed as straight as possible. It should be suitably anchored to prevent movement during the killing operation. The choke should have pressure ratings at least equal to the preventer stack and should meet all pressure testing specifications imposed on the preventers. It should divert flow to one of several areas including a burning pit, the reserve pit, a mud pit, or overboard a drilling vessel when applicable. The manifold should control pressures by using one of several chokes. Some of the conditions that the manifold may be called upon to work under are a variety of fluids such as mud, oil, water, or gas, high pressures, upstream flow rates, downstream velocities, and obstructions in the produced fluids such as sand, shale, 01 pipe protector rubbers. The choke manifold is an arrangement of valves, lines, and chokes designed to control the flow of mud and kick fluids from the annulus during the killing process. The preventer may be a low-pressure sphcrical preventer or some type of diverter bag used to direct the flow into the lines.Ĭhoke Manifold. Angles and bends should be minimized in the diveiter lines to avoid unnecessary restrictions. The lines should be as large as possible with a suggested minimum ID of 6 in. 16-68 Typical diverter stack (Courtesy PennWell Publishing) Close bag ''Open valves Open bag ^' Close valves fnr" " - Preventer valveįig.
